In dip coating, wettability to a coated material is important.
Naturally, dip coating is impossible if a coating liquid repels the surface of a coated material.
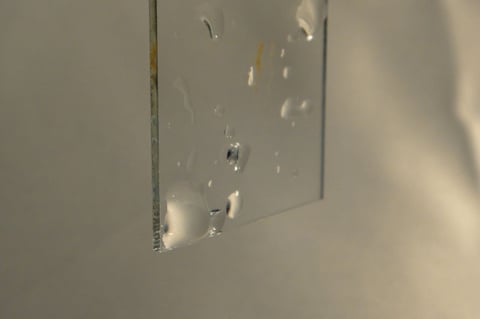
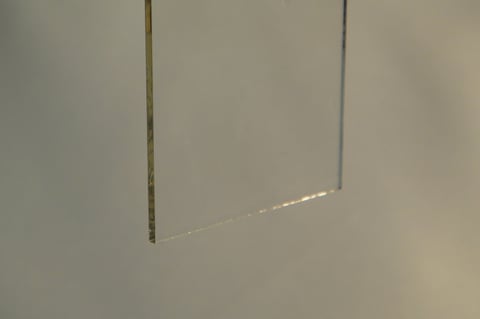
Modified by UV-Ozon Cleaner ASM401N
"High wettability" means that …
When a drop of liquid is dropped on the surface of a solid, if the wettability is low, the liquid will look like [Figure 1] (a), and if the wettability is high, the liquid will spread as shown in [Figure 1] (c).
In dip coating, the relationship between a solid and liquid is preferable as in (c).
This phenomenon is highly dependent on the properties of a solid surface and a liquid surface under conditions where there is no foreign matter adhering to a solid surface (a solid surface has been thoroughly cleaned).
[Figure 2] shows how the force relationships in the directions indicated by the three arrows are balanced on a solid surface. In this case, the following equation (Young's equation) is holds.
γSV=γSL+γLV COS・θ
γSV : Surface tension (surface free energy) of a solid
γLV : Surface tension of a liquid
γSL : Interfacial tension between a solid and liquid
θ : contact angle
The closer θ approaches 0°, the higher the wettability.
Liquids | Surface tension(mN/m) |
---|---|
Water | 72.75 |
Hexane | 18.4 |
Methanol | 22.5 |
Ethanol | 22.55 |
MEK | 24.6 |
Benzene | 28.9 |
Mercury | 486 |
Table A Surface Tension of Typical Liquids (at 20°C environment)
When a solid (a coated material) are identical, if the surface tension (γLV) of a liquid is large, θ will be large, which means the wettability is low (not suitable for dipping).
Table A shows that organic solvents have higher wettability than water soluble.
Also, when a liquid is identical, the small surface tension (γSV) of a solid (a coated material) indicates the wettability is low.
Table B shows that metals and glass have high surface tension and the wettability is high, while plastics and other resins have low surface tension and the wettability is low. Therefore, when dip coating plastics, surface modification is necessary to improve wettability.
Materials | Surface tension (mN/m) |
Temperature ℃ |
---|---|---|
Polypropylene | 23 | - |
Polytetrafluoroethylene | 18 | - |
PMMA | 37 | - |
Na2SiO2 (glass) | 310 | 1,000 |
Mercury | 486 | 20 |
Aluminum | 900 | 700 |
Copper | 1,120 | 1,128 |
Iron | 1,530 | 1,700 |
Table B Surface free energy of typical materials
What is surface modification?
Surface modification methods include UV irradiation with low-pressure mercury lamp (253.7 nm, 184.9 nm), excimer irradiation (172 nm), plasma surface modification, and corona treatment.
In this article, we will explain ultraviolet irradiation using low-pressure mercury lamp, which is one of the most typical types of surface modification.
Active oxygen formed by UV irradiation collide with a substrate surface, cleave the molecular chains of the surface layer, and then react with the cleaved molecules to form new functional groups (OH, CHO, COOH, etc.). These functional groups are highly hydrophilic and compatible with paints, adhesives, coating liquid, etc., resulting in a dramatic improvement and enhancement of adhesion.
Thus, before dip coating, it is possible to increase the surface tension (γSV) of a solid (to be coated) to improve wettability and make coating easier.